3D Printing Phoenix, or additive manufacturing (AM), is a process that builds objects by stacking and fusing layers of materials. It’s used to create everything from prototypes and models to finished products.
The technology allows manufacturers to design and build prototypes more quickly, speeding up product development. It also enables production to be moved closer to the point of demand, cutting logistics costs and carbon emissions.
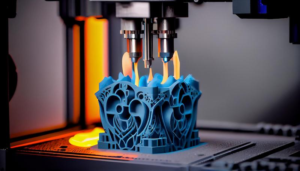
Rapid prototyping bridges the gap between idea and realization by allowing companies to test and refine product concepts before committing to full-scale production. This process enables design teams to save time and money by making fewer mistakes during the early stages of product development. In addition, it provides an opportunity to test user feedback and ensure that designs meet engineering requirements.
Prototypes can be digital or physical. The first step of creating a prototype involves designing a conceptual 3D model using a CAD software program. The resulting STL file can be printed by a 3D printer to create a physical prototype. The result is often rough, and may look like wire spaghetti or a makeshift object. However, this type of prototype is not meant to be visually appealing; it’s simply a way to test the functionalities and mechanical properties of a new product concept.
Another popular method for producing a rapid prototype is by using injection molding, CNC machining or vacuum casting. These processes can produce a prototype that more closely resembles the final product. However, these types of prototypes can be expensive and time-consuming to devePrintingprinting is a great alternative to these other methods of prototyping because it’s faster and more affordable. AdditionaPrintingprinting offers a wide variety of materials, including metals, plastics and ceramics. Depending on the type of 3D printing process used, a prototype can be made in either solid or hollow form.
A well-executed rapid prototype can significantly accelerate the design and testing phase, allowing engineers to bring a quality product to market in a fraction of the time it would take using traditional manufacturing techniques. This streamlined process also reduces the risk of costly errors during production, which can set back production schedules and increase overall costs.
The key to successful rapid prototyping is to set clear objectives from the outset. Identify what you want to find out from the test, and include all relevant stakeholders in the planning process. This helps to prevent oversights and avoid arguments over different features or decisions. It also ensures that the prototype is used to test the most critical elements of a design.
Additive Manufacturing
Additive manufacturing (AM) is a production method that joins materials by layering them in order to construct an object from a computer-aided design (CAD) model. This is a different approach to the traditional manufacturing process, which uses tools to cut or shape parts.
Adding material to the part in layers allows designers to create complex geometries that would be impossible or very difficult to produce using other methods. This freedom in geometry is a major benefit of AM, and it enables engineers to design for the desired end product rather than designing for the manufacturing process.
This is a key distinction that separPrintingprinting from many other processes, such as casting or forging. In addition, additive manufacturing offers the potential to reduce lead times, which can significantly decrease the time between concept and completion of a new product or service.
Although the term ‘3D printing’ is most often associated with maker culture, hobbyists and amateurs, desktop printers and low-cost materials like acrylonitrile butadiene styrene (ABS), it is increasingly being used by commercial and industrial businesses. These users are typically involved in product prototyping, small- to medium-scale series production and some limited custom manufacturing.
Larger companies that are engaged in full production are also exploring the usPrintingprinting, with a particular focus on using the technology to improve quality and efficiency in the supply chain. This can include everything from tooling for production line assembly to replacement parts for existing products.
One example is jewelry. Here, the 3D printed pattern can be made directly from the CAD data or it can be printed as a mold for investment casting, where molten metal is poured around the printed pattern to form a solid cast. The resulting piece can then be polished, finished and polished to achieve the desired appearance and functionality of the final product.
There are also numerous examples of 3D printed medical and healthcare devices, including surgical instruments and implants. This is particularly exciting, because it demonstrates that the technology is now mature enough for clinical use and is becoming a viable alternative to traditional surgical techniques.
Bioprinting
A bioprinter works by positioning living cells into 3D structures to form living tissue or organs. This technology could be used to manufacture medical implants and prosthetics. It can also be used to make customized drug delivery systems. The potential of the technology in regenerative medicine is tremendous.
Bioprinting can use a variety of different materials. These materials include polymers, metals and ceramics. In order to print the required material, it must be preformed or processed to have the correct texture and mechanical properties. There are a variety of printing methods, such as material extrusion, inkjet 3D bioprinting and stereolithography. These processes are designed to give the final printed piece its strength and appearance, as well as to enable it to be printed in layers.
Before thePrintingprinting can start, a model must be created. This can be done either using an external CAD program or, in some printers, it can be done directly within the software interface. Once the model is in place, a process called cell seeding takes place. In this step, the required cells are isolated and captured (if necessary) from a biopsy of the intended body part, and then multiplied through a special culturing process. Once the appropriate number of cells is available, they are mixed into a bioink.
This bioink is then used by the printer to print out the desired structure. Depending on the project, this can be as simple as printing out a small, fully functional heart or as complex as creating a whole new organ. For example, a team of researchers has recently succeeded in printing out a tiny human liver. This’mini-liver’ has the ability to produce vital proteins, store vitamins and secrete bile.
While the technology has yet to be successfully used in humans, the potential of the bioprinting technology in regenerative medicine is immense. It can help reduce the time that is needed to develop a drug, as it can provide access to more biorelevant models earlier in the development process. This in turn means that fewer patients will need to be involved in costly, risky human trials.
Digital Manufacturing
Digital manufacturing aims to reduce the time it takes for a product to go from idea to finished consumer good. It involves using digital modelling software to design tools and machinery, factory floor layouts, production flows, and other factors that enable faster ad-hoc prototyping and iteration. The technology can then be used to build a prototype of a piece of equipment or a new product, which can be tested in the real world to identify problems or to improve aesthetics.
The first step is to create a 3D digital model of the desired object. This is typically done through a computer-aided design (CAD) system. Ideally, the design will be optimisedPrintingprinting, also known as Design For Manufacture (DFM). This includes accounting for size and geometry limitations, material properties (e.g. sintering, heat resistance and strength), tolerance and surface finish requirements.
Once the design is ready, it must be “sliced” into layers suitable for the chosen printer. This may be accomplished in a number of ways, depending on the process and software. The sliced file is then fed into the printer, which builds the object layer by layer. It takes time Printingprinting to complete, but this depends on the size and quality of the item.
For example, a high-resolution, detailed model might take several hours or days to print, while a lower-resolution, simpler shape might only take minutes. Once the item is printed, it must be removed from the printer, if necessary, cleaned, and if it is made of metal, treated to remove any residual support structures or blemishes.
Jewelers are another group of professionals who benefit from the ability to quickly and inexpensively produce complex and unique designs using metal 3D printing. It offers them a quick alternative to the traditional tools they use such as CNC machining and lost-wax casting.
It is also possible to use this technology to produce replacement parts for existing machinery and equipment, enabling a business to save money by not having to replace obsolete or worn out components. It can also be useful for training and education purposes, enabling people to work on or operate complicated machinery without having to travel to the manufacturer of the machine.